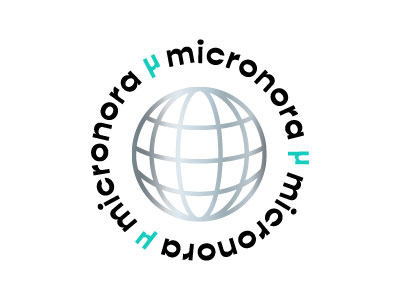
La dictature du temps réel
Les entreprises microtechniques, comme toutes les entreprises d’ailleurs, sont confrontées à des défis, souvent contradictoires. Elles doivent produire toujours plus, mais par petits lots, des produits personnalisés, avec une qualité proche de la perfection et des coûts en baisse permanente. Ce qui s’apparente à la quadrature du cercle et leur impose une connaissance parfaite de l’état du système de production. Autrement dit, elles sont soumises à la dictature du temps réel. Que produisent les machines, comment se déroule le processus de fabrication, quand interviendra un incident qui arrêtera la production ?
Toutes ces questions taraudent jour et nuit les responsables de production qui doivent y répondre en temps utile. La technologie vient à leur secours. Aujourd’hui accéder à des informations de production tous azimuts et piloter la production à distance via des réseaux sécurisés devient possible avec les nouveaux moyens de communication, smartphones et autres tablettes. Même les constructeurs de machines-outils s’en inspirent pour mettre au point des interfaces plus simples, plus efficaces.
Lauréate du prix Automatisation/Industrie 4.0 à l’EMO 2017 à Hanovre (Allemagne), la commande numérique DATRON next du constructeur de machines-outils d’usinage à grande vitesse (UGV) éponyme n’a rien à envier aux smartphones. Son secret : l’association d’une interface tactile à une caméra et un palpeur 3D (capteur XYZ) qui permet de paramétrer rapidement et simplement tous les usinages.
L’association d’une tablette avec un système d’analyse en temps réel de données est en pointe de mire des acteurs importants du monde industriel. Apple annonce ainsi un accord avec General Electric (GE) pour fournir aux usines des solutions qui permettent le pilotage d’une ligne de fabrication avec un iPad. Les deux partenaires proposeront un kit de développement d’applications mobiles tournant sur iOS. Les informations seront fournies par la plateforme Predix de GE qui gère les objets connectés dans les usines et est capable d’analyser en temps réel des données multiples.
D’autres grands acteurs industriels comme Siemens, Dassault Systèmes ou Bosch proposent ou développent des solutions similaires. D’abord baptisé Cloud for industry, en 2015, puis MindSphere, la plate-forme de Siemens offre les bénéfices du big data à l’industrie. Grâce à des applications mobiles et des services numériques, elle doit permettre l’enregistrement, le traitement et l’analyse des énormes volumes d’informations générés sur un site de production. L’intégration des données des systèmes de production dans des applications ouvre en effet la voie à l’amélioration sensible des performances. L’ordinateur industriel qui permet de collecter les données issues du terrain et de les transmettre de manière chiffrée au cloud est l’un des produits de Siemens qui s’intègre dans cette offre. L’usine connectée est désormais en marche…
Source photo : Datron